Industrial Engineering: Transforming Job Design at Windy City
How industrial engineers transform job design
Organizations invariably seek ways to improve efficiency, productivity, and employee satisfaction. For windy city, hire an industrial engineer represent a strategic move toward optimize job design across their operations. These specialized professionals bring unique skills and methodologies that can transform how work gets do.
Industrial engineers apply scientific principles to analyze, design, and improve systems that involve people, equipment, materials, and processes. Their expertise prove specially valuable when companies need to overhaul their job design approaches to meet change market demands.
Scientific approach to workflow analysis
Industrial engineers employ systematic methodologies to evaluate exist job structures. At windy city, this analysis would begin with comprehensive workflow mapping to identify bottlenecks, redundancies, and inefficiencies in current processes.

Source: nawindpower.com
Through time motion studies, engineers can quantify each task component, measure incisively how long different operations take and identify opportunities for improvement. This data drive approach eliminate guesswork and provide concrete metrics for decision-making.
For example, an industrial engineer might discover that windy city employees spend excessive time on non value add activities or face unnecessary physical strain due to unwell design workstations. These insights form the foundation for target improvements.
Ergonomic workplace design
One of the virtually immediate benefits an industrial engineer bring to windy city involve ergonomic improvements. Proper ergonomic design reduce physical strain, prevent workplace injuries, and enhance overall productivity.
Industrial engineers analyze job tasks through an ergonomic lens, consider factors like:
- Physical movements require
- Force exertion patterns
- Repetitive motion risks
- Environmental factors (lighting, noise, temperature )
- Workstation layout and tool design
By implement ergonomic principles, windy city can expect reduced absenteeism due to injuries, lower healthcare costs, and improve employee comfort. Workers who experience less physical strain course maintain higher productivity levels throughout their shifts.
Standardization and work balancing
Inconsistent work methods create inefficiencies and quality variations. Industrial engineers develop standardized work procedures that establish the nigh efficient methods for complete tasks.
At windy city, standardization would involve:
- Document best practices
- Create detailed work instructions
- Establish time standards for task completion
- Design training programs base on optimal methods
Beyond standardization, industrial engineers excel at work balancing — distribute tasks equally across workstations or team members to eliminate bottlenecks and idle time. This balance act ensure smooth workflow and maximize resource utilization.
For instance, if certain departments at windy city regularly face backlogs while others have excess capacity, an industrial engineer can redesign job responsibilities to create more balanced workloads across the organization.
Human factors integration
Unlike strictly technical approaches to efficiency, industrial engineering consider human factors equally central to job design. These professionals understand that jobs must be design to accommodate human capabilities and limitations.
For windy city, this human center approach mean jobs would be design consider:
- Cognitive load and information processing requirements
- Attention spans and fatigue factors
- Decision make responsibilities
- Social interaction need
- Skill development opportunities
By account for these human factors, industrial engineers create jobs that not solely maximize efficiency but besides enhance job satisfaction and employee engagement. This dual focus distinguishes industrial engineering from approaches that prioritize technical efficiency without consider human elements.
Process optimization through lean principles
Many industrial engineers specialize in lean methodologies — systematic approaches to eliminate waste while deliver value. For windy city, implement lean principles could dramatically improve job design by remove non value add activities.
Key lean concepts an industrial engineer might implement include:
-
Value stream mapping:
Visualize the entire process to identify value add, and non value add steps -
5s workplace organization:
Consistently organize workspaces for efficiency and effectiveness -
Mistake proofing (ppokeyyoke):
Designing processes to prevent errors before they occur -
Continuous flow:
Eliminate batch processing and create smooth workflows -
Pull systems:
Produce base on actual demand preferably than forecasts
These principles help create jobs that focus on value creation while eliminate wasteful activities. Employees benefit from more meaningful work that contribute direct to organizational goals kinda than bureaucratic busywork.
Data drive decision make
Industrial engineers excel at collect and analyze operational data to inform job design decisions. At windy city, this data drive approach ensure that changes to job structures are base on evidence preferably than assumptions.
Through techniques like statistical process control, simulation modeling, and operations research, industrial engineers can:
- Predict the impact of propose changes before implementation
- Identify optimal staffing levels for different operations
- Determine the virtually efficient sequence of tasks
- Quantify performance improvements from job redesign
This analytical rigor help windy city avoid costly trial and error approaches to job redesign. Alternatively, changes can be implemented with confidence, back by solid data and prove methodologies.
Technology integration for enhanced job design
Modern industrial engineers bring expertise in integrate technology into job design. For windy city, this might involve implement:
- Digital work instructions and visual management systems
- Automation of repetitive or physically demand tasks
- Sensor base monitoring for real time feedback
- Collaborative robotics to assist workers
- Digital tools for communication and knowledge sharing
By thoughtfully incorporate technology, industrial engineers can design jobs that leverage human strengths while use technology to compensate for limitations. This approach create more engaging work environments where technology serve as an enabler instead than a replacement for human workers.
Cross-functional collaboration enhancement
Industrial engineers view organizations as interconnect systems quite than isolated departments. This perspective prove invaluable for windy city in design jobs that facilitate cross-functional collaboration.
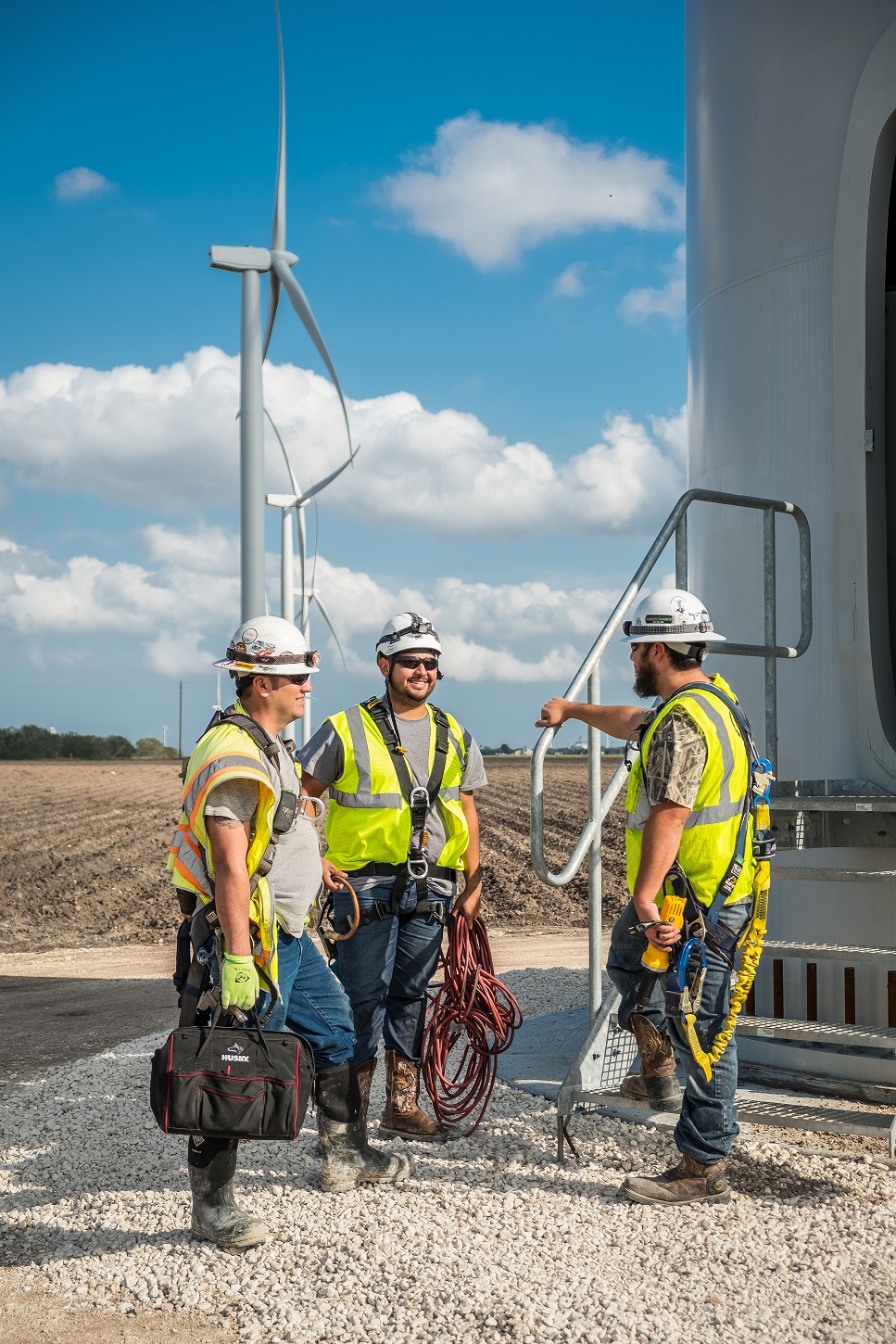
Source: globalwindsafety.org
Through techniques like value stream mapping and process flow analysis, industrial engineers identify handoff points between departments and design jobs that minimize information loss and delays at these critical junctures.
For example, an industrial engineer might redesign job responsibilities to create liaison roles that bridge communication gaps between engineering and production teams. Instead, they might implement visual management systems that make work status transparent across departments.
These systems think approach ensure that job design support organizational goals kinda than optimize departmental performance at the expense of overall outcomes.
Performance measurement and continuous improvement
Industrial engineers establish robust performance measurement systems that align with job design. For windy city, this mean creates metrics that:
- Focus on both process and outcome measures
- Balance efficiency with quality and safety
- Provide timely feedback to employees
- Support continuous improvement efforts
Beyond establish metrics, industrial engineers implement continuous improvement methodologies that empower employees to identify and resolve issues in their work processes. This creates a dynamic environment where job design evolve base on frontline insights quite than remain static.
Through structured problem solve approaches like PDA ((lan do check act ))ycles, employees become active participants in refine their job designs instead than passive recipients of toptop-downrectives.
Training program development
Yet the advantageously design jobs require effective training systems to ensure employees can perform to standards. Industrial engineers excel at develop training programs that:
- Break complex tasks into manageable learning modules
- Incorporate adult learning principles
- Use visual aids and hands on practice
- Include measurable competency assessments
- Support knowledge retention and application
For windy city, these structured training approaches ensure that job redesign efforts translate into actual performance improvements instead than create confusion or resistance.
Change management and implementation
Peradventure virtually critically, industrial engineers bring expertise in manage the human side of change. Job redesign needs to create disruption, and successful implementation require thoughtful change management.
Industrial engineers typically employ strategies like:
- Stakeholder analysis and engagement planning
- Clear communication of the rationale for changes
- Pilot implementations to demonstrate benefits
- Phase rollouts to manage disruption
- Feedback mechanisms to address concerns
This change management expertise help windy city overcome resistance and achieve buy in for job design improvements. Preferably than impose changes, industrial engineers create collaborative processes that incorporate employee input while maintain focus on organizational objectives.
Measurable benefits for windy city
By hire an industrial engineer to improve job design, windy city can expect numerous quantifiable benefits:
-
Productivity improvements:
Typically, 15 30 % through elimination of wasteful activities and process optimization -
Quality enhancements:
Reduced defect rates through error proofing and standardized work -
Reduced turnover:
Improved job satisfaction through ergonomic and human center design -
Lower injury rates:
Decreased workers’ compensation costs through ergonomic improvements -
Faster onboarding:
More effective training through standardized work and clear instructions -
Innovation capacity:
Freed employee time for creative problem solve kinda than firefight
These benefits compound over time as continuous improvement becomes embed in the organizational culture. What begins as tactical job redesign evolve into a strategic advantage through ongoing optimization.
Conclusion: strategic investment in operational excellence
For windy city, hire an industrial engineer represent more than precisely a staffing decision — it’s a strategic investment in operational excellence. Through scientific analysis, human center design principles, and systematic improvement methodologies, industrial engineers transform how work gets do.
The result job designs balance multiple objectives: efficiency, quality, employee satisfaction, and adaptability to change conditions. Instead than optimize for a single variable, industrial engineers create holistic solutions that support sustainable performance improvement.
As organizations face increase pressure to do more with less while maintain employee engagement, the specialized expertise of industrial engineers become progressively valuable. For windy city, this expertise could be the key to unlock new levels of performance while create a more satisfying work environment for employees at all levels.